I. Definition and basic concepts
Fused quartz, also known as fused quartz, is an amorphous silicon dioxide material formed by melting extremely pure natural quartz (usually crystal) or synthetic quartz at high temperature and then rapidly cooling it. Its chemical composition is mainly SiO₂, and the theoretical purity can reach more than 99.99%. Compared with crystalline quartz, fused quartz does not have obvious crystal structure and grain boundaries due to its disordered atomic structure, which gives it many unique physical and chemical properties.
II. Characteristics
(I) Physical properties
1. Optical properties
High transmittance: Fused quartz has excellent optical transmittance in the ultraviolet, visible and near-infrared bands. For example, in the wavelength range of 190-2500nm, its transmittance can reach more than 90%. This property makes it an ideal material for optical components such as optical lenses, optical windows, and optical fibers.
Low dispersion: The dispersion coefficient of fused quartz is extremely low, which means that the speed difference of light of different wavelengths when propagating in it is small, so it can effectively reduce chromatic aberration and improve imaging quality in optical systems. This feature is particularly important in high-end optical instruments such as microscopes and telescopes.
2. Thermal properties
Low thermal expansion coefficient: The thermal expansion coefficient of fused quartz is very low. In the temperature range of 20-1000℃, its average linear expansion coefficient is only about 0.5×10⁻⁶/℃. This allows it to maintain dimensional stability in an environment with drastic temperature changes and is not prone to thermal deformation. Therefore, fused quartz is widely used in fields with extremely high requirements for thermal stability, such as aerospace, astronomy, etc.
High heat resistance: The melting point of fused quartz is as high as 1713℃, and it has good heat resistance and can withstand high temperature environments without softening or melting. This makes it an important material in high-temperature furnaces, refractory materials and other fields.
3. Mechanical properties
High hardness: The Mohs hardness of fused quartz is about 7, which has a high hardness and can resist a certain degree of wear and scratches. This makes it perform well in some applications that require wear resistance, such as grinding media in mechanical processing, ceramic molds, etc.
High strength: Although fused quartz is a brittle material, it still has high compressive strength and flexural strength at room temperature. Through appropriate processing and treatment, its strength can be further improved to meet the needs of different engineering applications.
4. Electrical properties
High insulation: Fused quartz is an excellent electrical insulator with a resistivity of up to 10¹⁴ - 10¹⁶Ω・cm. This makes it widely used in the field of electronics and electrical appliances to manufacture insulating parts, such as insulators, electron tube housings, etc.
Low dielectric constant: Fused quartz has a low dielectric constant and has good electrical properties in the microwave and radio frequency bands. This makes it an ideal material for manufacturing microwave devices, high-frequency circuit substrates, etc.
(II) Chemical properties
1. Chemical stability
Fused quartz has extremely high chemical stability and hardly reacts with any acid (except hydrofluoric acid), alkali, salt or other chemical substances. This makes it widely used in the chemical industry, food industry, pharmaceutical industry and other fields to manufacture corrosion-resistant equipment, pipelines, containers, etc.
2. Radiation resistance
Fused quartz has good tolerance to high-energy radiation (such as γ rays, X-rays, etc.) and will not undergo obvious physical and chemical changes in a radiation environment. This characteristic makes it have important application value in the fields of nuclear industry, medical radiation protection, etc.
III. Production method
(I) Electric fusion method
Electrofusion method is one of the most commonly used methods for producing fused quartz. This method uses high-purity natural quartz sand or crystal as raw material, puts it into a graphite crucible or electric melting furnace, and melts the quartz raw material through the high temperature (usually above 2000℃) generated by the power of the electrode. The molten quartz liquid flows out through the outlet at the bottom and is quickly cooled by a water cooling device to form an amorphous fused quartz block. The fused quartz produced by the electric melting method has high purity and stable quality, but the energy consumption is large and the production cost is relatively high.
(II) Gas refining method
The gas refining method is a method of producing fused quartz using the principle of vapor deposition. This method uses silicon halides such as silicon tetrachloride (SiCl₄) as raw materials, gasifies them and mixes them with hydrogen and oxygen, and hydrolyzes them in a high-temperature flame (usually at 1800-2000℃) to produce silicon dioxide particles. These particles are deposited and melted in the flame to form fused quartz. The fused quartz produced by the gas refining method has extremely high purity, reaching more than 99.999%, and has good optical properties and microstructure. However, the gas refining method has complex equipment, difficult production process control, and relatively low output. It is mainly used to produce high-quality fused quartz products required in high-end optical and electronic fields.
(III) Plasma method
The plasma method is a new type of fused quartz production method developed in recent years. This method uses high-temperature plasma generated by a plasma torch to instantly heat the quartz raw material to a molten state. The plasma method has the advantages of fast heating speed, high temperature and low energy consumption, and can produce high-quality fused quartz. At the same time, this method can also achieve precise control of the microstructure and performance of fused quartz, providing a new way to develop new high-performance fused quartz materials. However, the equipment investment of the plasma method is large and the technical difficulty is high. It is still in the research and development stage.
IV. Application fields
(I) Optical field
1. Optical lenses and lenses: Due to the characteristics of high transmittance, low dispersion and good optical uniformity, fused quartz is widely used in the manufacture of various optical lenses and lenses, such as camera lenses, telescope lenses, microscope objective lenses, etc. These optical components can provide clear and high-resolution images, meeting the demand for high-quality optical materials in the field of optical imaging.
2. Optical windows and prisms: Fused quartz also occupies an important position in the manufacture of optical windows and prisms. Optical windows are used to protect the optical components inside the optical system from the influence of the external environment, and are required to have high transmittance and good optical properties. Optical windows made of fused quartz can meet these requirements and are widely used in aerospace, military, astronomical observation and other fields. Prisms are used for light refraction, reflection and splitting in optical systems. The low dispersion and high optical stability of fused silica enable prisms to accurately control the propagation direction and angle of light and improve the performance of optical systems.
3. Optical fiber: Optical fiber is the core component of modern optical communication technology, and fused silica is the main material for manufacturing optical fiber. Fused silica optical fiber has the advantages of low loss, high bandwidth, and anti-electromagnetic interference, and can achieve high-speed and large-capacity data transmission. At present, fused silica optical fiber has been widely used in long-distance communication, metropolitan area network, local area network, fiber-to-the-home and other fields, becoming an indispensable infrastructure for the information society.
(II) Electronic field
1. Semiconductor manufacturing: In the semiconductor manufacturing process, fused silica is widely used to manufacture photolithography masks, wafer carriers, reaction chamber components, etc. The photolithography mask is a key component in the semiconductor lithography process, which requires high-precision pattern transfer capabilities and good dimensional stability. Due to its low expansion coefficient and high flatness, fused silica can meet the strict requirements of the photolithography mask and ensure high precision and high yield of semiconductor chip manufacturing. Wafer carriers are used to carry and transport semiconductor wafers and need to maintain stable performance in harsh environments such as high temperature and high vacuum. The excellent thermal and mechanical properties of fused quartz make it an ideal material for wafer carriers. In addition, the application of fused quartz in semiconductor reaction chamber components can effectively resist chemical corrosion and high temperature environments, ensuring the stability and reliability of the semiconductor manufacturing process.
2. Integrated circuit packaging: With the continuous development of integrated circuit technology, the performance requirements for packaging materials are getting higher and higher. Fused quartz is widely used in the field of integrated circuit packaging due to its high insulation, low dielectric constant and good thermal stability. It can be used as a packaging substrate, chip carrier and other materials to effectively protect the chip from the influence of the external environment, while realizing the electrical connection between the chip and the external circuit. Integrated circuits packaged with fused quartz have good electrical performance and reliability, and can meet the needs of modern electronic products for high performance and miniaturization.
3. Electronic components: Fused quartz is also used to manufacture various electronic components, such as capacitors, resistors, oscillators, etc. In capacitors, fused quartz is used as a dielectric material to improve the insulation performance and capacitance stability of capacitors. In resistors, fused quartz can be used as the base material of resistors to improve the heat resistance and stability of resistors. In oscillators, the high frequency stability and low temperature coefficient of fused quartz make it a key material for manufacturing high-precision quartz crystal oscillators. These electronic components are widely used in electronic communications, computers, automotive electronics and other fields, providing important support for the development of modern electronic technology.
(III) High-temperature industrial field
1. Refractory materials: Fused quartz has a high melting point, high heat resistance and good chemical stability, and is an important raw material for manufacturing refractory materials. Refractory products made of fused quartz, such as quartz bricks, quartz crucibles, quartz sleeves, etc., are widely used in high-temperature furnaces such as the glass industry, steel industry, and ceramic industry. These refractory products can withstand the erosion of high-temperature environments, ensure the normal operation of furnaces, and improve production efficiency and product quality.
2. Glass manufacturing: In the glass manufacturing process, fused quartz, as an important glass raw material, can improve the purity, transparency and chemical stability of glass. At the same time, due to the low expansion coefficient of fused quartz, it can effectively reduce the thermal stress of glass products during heating and cooling, and reduce the risk of cracking of glass products. Therefore, fused quartz is widely used in the manufacture of high-end glass products, such as optical glass, electronic glass, heat-resistant glass, etc.
3. Ceramic industry: In the ceramic industry, fused quartz can be used as an additive to ceramic blanks to improve the performance of ceramics. It can reduce the sintering temperature of ceramic blanks, improve the density and mechanical strength of ceramics, and improve the thermal stability and chemical stability of ceramics. In addition, fused quartz can also be used to make ceramic molds. Due to its high hardness and good wear resistance, it can improve the service life and molding accuracy of ceramic molds.
(IV) Other fields
1. Aerospace field: Due to its excellent thermal stability, low weight and good mechanical properties, fused quartz is widely used in the aerospace field to manufacture aircraft structural components, engine components, thermal protection systems, etc. For example, in the leading edge of the aircraft wing, the engine air inlet and other parts, the use of fused quartz-based composite materials can effectively resist the scouring of high-speed airflow and the erosion of high-temperature environment, and improve the performance and safety of the aircraft.
2. Medical field: The chemical stability and biocompatibility of fused quartz make it have certain application value in the medical field. It can be used to manufacture medical devices such as syringes, infusion sets, culture dishes, etc. These medical devices can effectively avoid chemical reactions with drugs or biological samples, ensuring the safety and accuracy of the medical process. In addition, fused quartz can also be used as a dental restoration material. Due to its good optical properties and wear resistance, it can produce restorations similar to natural teeth, improving the patient's oral beauty and chewing function.
3. Jewelry field: After special processing, fused quartz can be made into various exquisite jewelry, such as crystal jewelry, glass crafts, etc. These jewelry are crystal clear and have good gloss, and are deeply loved by consumers. At the same time, due to the relatively low cost of fused quartz, these jewelry have a high cost performance and are competitive in the market.
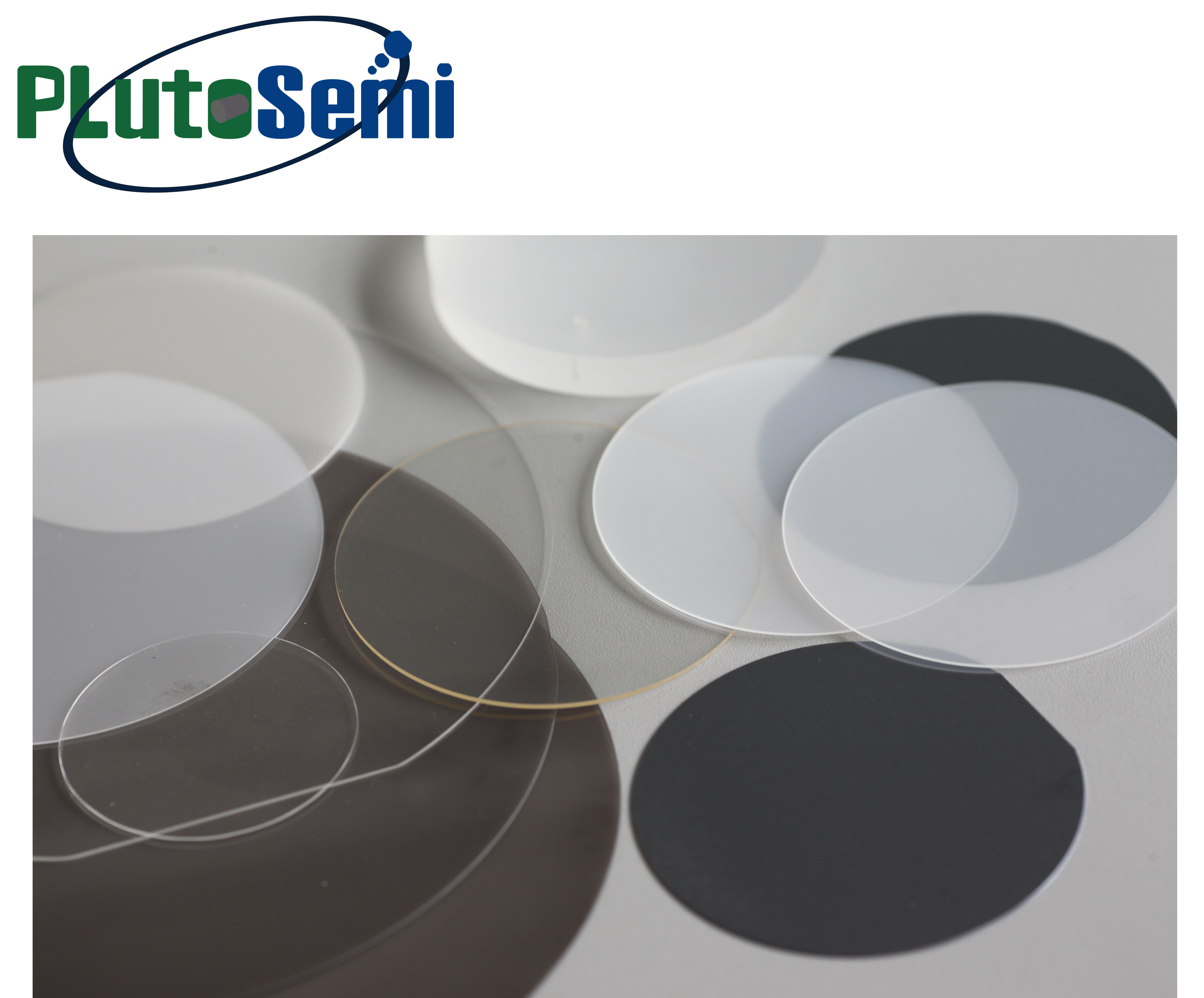