I. Introduction
Silicon carbide (SiC), as a compound semiconductor material with unique properties, occupies a pivotal position in the development of modern science and technology. Since its discovery in the 19th century, with the continuous deepening of material preparation technology and application research, silicon carbide has gradually expanded from the initial abrasive field to many high-end technology fields such as electronics, energy, and aerospace, becoming a key basic material to promote the technological upgrading and innovative development of related industries.
II. Basic Information
Silicon carbide is a compound formed by the covalent bonding of two elements, silicon (Si) and carbon (C), and its chemical formula is SiC. In terms of crystal structure, silicon carbide has a variety of crystal forms, among which the most common ones are cubic system (β-SiC) and hexagonal system (α-SiC). Silicon carbide of different crystal forms has certain differences in physical and chemical properties, which also provides more possibilities for its selection in different application scenarios.
III. Characteristics
1.High hardness: The Mohs hardness of silicon carbide is as high as 9.5, second only to diamond, which makes it have excellent wear resistance and is often used to make abrasives, cutting tools, etc. In grinding tools such as grinding wheels and sandpaper, silicon carbide abrasives can efficiently grind various metal and non-metal materials, significantly improving processing efficiency and surface quality.
2.High thermal conductivity: Its thermal conductivity is comparable to that of copper, and even higher in some cases. This property makes silicon carbide an ideal material for heat dissipation in electronic equipment. For example, in high-power electronic devices, the use of silicon carbide heat sinks can quickly conduct heat away, effectively reduce the temperature of the device, improve its working stability and reliability, and extend its service life.
3.High chemical stability: Silicon carbide exhibits extremely strong chemical stability in harsh environments such as high temperature, strong acid, and strong alkali. In the chemical industry, reactors, pipelines and other equipment made of silicon carbide can withstand the erosion of various corrosive media, ensuring the safe and stable operation of the production process and reducing equipment maintenance costs.
4.Wide bandgap: Compared with traditional silicon semiconductors, silicon carbide has a wider bandgap. This means that silicon carbide devices can operate at higher temperatures, higher voltages, and higher frequencies. In the field of power electronics, power devices based on silicon carbide can achieve higher power density and lower energy loss, providing strong support for the development of new energy vehicles, smart grids and other industries.
IV. Preparation method
1.High temperature synthesis method: This is the earliest and most commonly used method for preparing silicon carbide. Usually, quartz sand (SiO₂) and coke (C) are mixed in a certain proportion and heated to 2000-2500℃ in a high-temperature electric furnace to produce a chemical reaction SiO₂ + 3C → SiC + 2CO↑ to generate silicon carbide. This method is relatively simple, but the energy consumption is high, and the product purity and crystal quality are greatly affected by the purity of the raw materials and the reaction conditions.
2.Chemical vapor deposition (CVD): In a high-temperature reactor, gaseous compounds containing silicon and carbon elements (such as silane SiH₄ and methane CH₄) are chemically reacted on the substrate surface, and silicon and carbon atoms are deposited and crystallized on the substrate to form a silicon carbide film. The CVD method can accurately control the thickness, composition and crystal structure of the silicon carbide film, and is suitable for preparing high-quality silicon carbide epitaxial wafers and is widely used in the field of semiconductor device manufacturing.
3.Sol-gel method: First, a gel containing silicon and carbon precursors is prepared through a sol-gel process, and then it is converted into silicon carbide by high-temperature sintering. This method has the advantages of low process temperature and easy control of composition and microstructure. It can be used to prepare silicon carbide ceramic-based composite materials, nano-silicon carbide powders, etc., but the preparation process is relatively complicated and the production efficiency is relatively low.
V. Application fields
1.Electronic field
(1)Power devices: Silicon carbide power diodes, MOSFETs and other devices have been widely used in on-board chargers, inverters and charging piles of new energy vehicles. Compared with traditional silicon-based power devices, silicon carbide devices can significantly improve system efficiency, reduce energy loss, and reduce equipment size and weight. In new energy vehicles, the use of silicon carbide power modules can increase the vehicle's cruising range by 5-10%, while significantly shortening the charging time.
(2) RF devices: In 5G communication base stations, silicon carbide-based RF devices can work stably at high power and high frequency, effectively improving the signal transmission power and coverage of base stations and improving communication quality.
2.Energy field
(1)Photovoltaic industry: Silicon carbide can be used as a substrate material and electrode material for photovoltaic cells to improve the photoelectric conversion efficiency and stability of the cells. In addition, in the power conversion system of photovoltaic power stations, the application of silicon carbide power devices can also help reduce system energy consumption and improve power generation efficiency.
(2) Nuclear energy field: Silicon carbide has good high temperature and radiation resistance, and can be used to manufacture fuel cladding and structural materials for nuclear reactors, improving the safety and operating life of reactors.
3.Mechanical field
(1)Wear-resistant parts: As mentioned above, the high hardness and wear resistance of silicon carbide make it an ideal material for manufacturing mechanical seals, bearings, nozzles and other wear-resistant parts. In the petrochemical, mining, metallurgical and other industries, these silicon carbide wear-resistant parts can withstand harsh working environments, greatly extend the service life of equipment, and reduce equipment maintenance and replacement costs.
(2)Cutting tools: Silicon carbide tools perform well in high-speed cutting, can efficiently cut high-hardness and high-strength materials, improve processing accuracy and surface quality, and are widely used in precision processing fields such as aerospace and automobile manufacturing.
4.Aerospace field
(1)Thermal structural materials: When a spacecraft reenters the atmosphere, the surface will be subjected to extremely high temperatures. Silicon carbide ceramic-based composites can be used to manufacture thermal protection systems and engine components of spacecraft due to their advantages of low density, high specific strength, high heat resistance and oxidation resistance, effectively reducing the weight of spacecraft and improving their performance and reliability.
(2)Aircraft engine components: High-temperature components of aircraft engines such as combustion chambers and turbine blades have extremely high requirements for high temperature resistance and high strength of materials. Silicon carbide-reinforced metal matrix composites can be used to manufacture these components, improve the thermal efficiency and thrust-to-weight ratio of the engine, and reduce fuel consumption.
VI. development trend
1. Reduce costs: With the continuous expansion of the silicon carbide application market, reducing production costs has become a key factor in promoting its large-scale application. In the future, by optimizing the preparation process, improving production efficiency, and developing new raw materials, it is expected to further reduce the cost of silicon carbide materials and devices and improve their market competitiveness.
2. Improve material quality: In the field of electronics, higher requirements are placed on the crystal quality, purity and consistency of silicon carbide materials. Developing advanced growth technology and defect control methods to prepare high-quality, large-size silicon carbide single crystal materials and epitaxial wafers will be one of the research focuses in the future.
3. Expand application areas: With the continuous advancement of science and technology, the potential application value of silicon carbide in emerging fields such as quantum communication, biomedicine, and extreme environment sensors will gradually be explored and developed, further expanding its application boundaries and bringing new opportunities for the development of related industries.
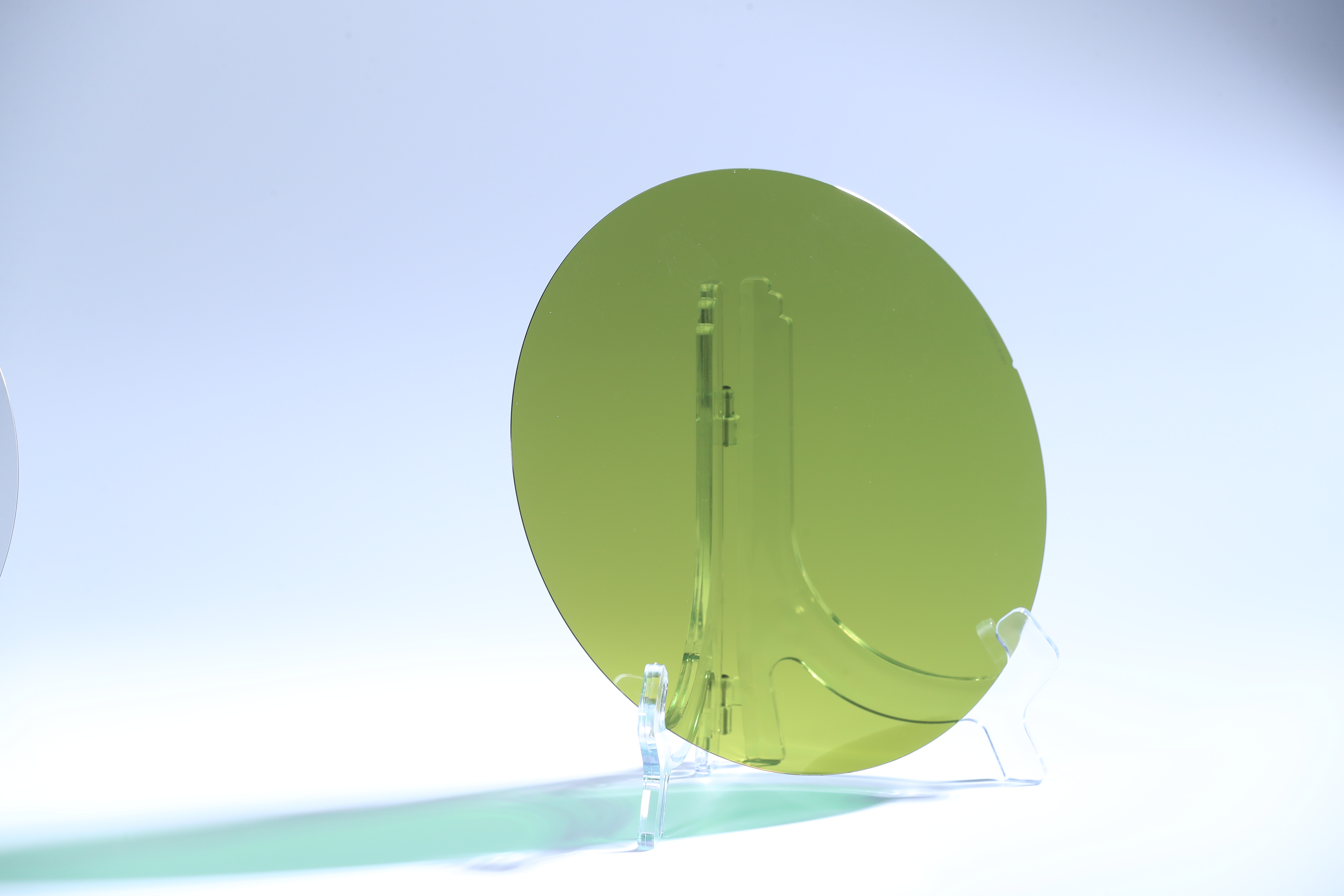